Contents
Product development in the fashion industry is an essential part of the overall manufacturing process. Planning ahead of time will ensure the success of your fashion business. Fashion product development is responsible for managing the entire product lifecycle, from concept to manufacturing. And its ultimate goal is to efficiently manage all stages of product creation.
In this blog post, we discuss the most important stages of fashion product development and how to manage them effectively using modern technologies.
Let's start with the definition of product development in fashion.
What is product development in fashion?
Product development in fashion is the process of designing, planning, and developing saleable products for the target consumer. The purpose of product development is to certify that the manufacturer understands and follows the specifications established to build a specific product.
Every fashion company's goal is to provide their customers with the best product possible at the most competitive price. Product development exists to achieve this goal. Product development's ultimate goal is to ensure customer satisfaction while minimizing returns.
5 main stages of product development in fashion
Product development in fashion consists of multiple steps that must be completed before finished goods is produced. Below are the most common steps in the product development process.
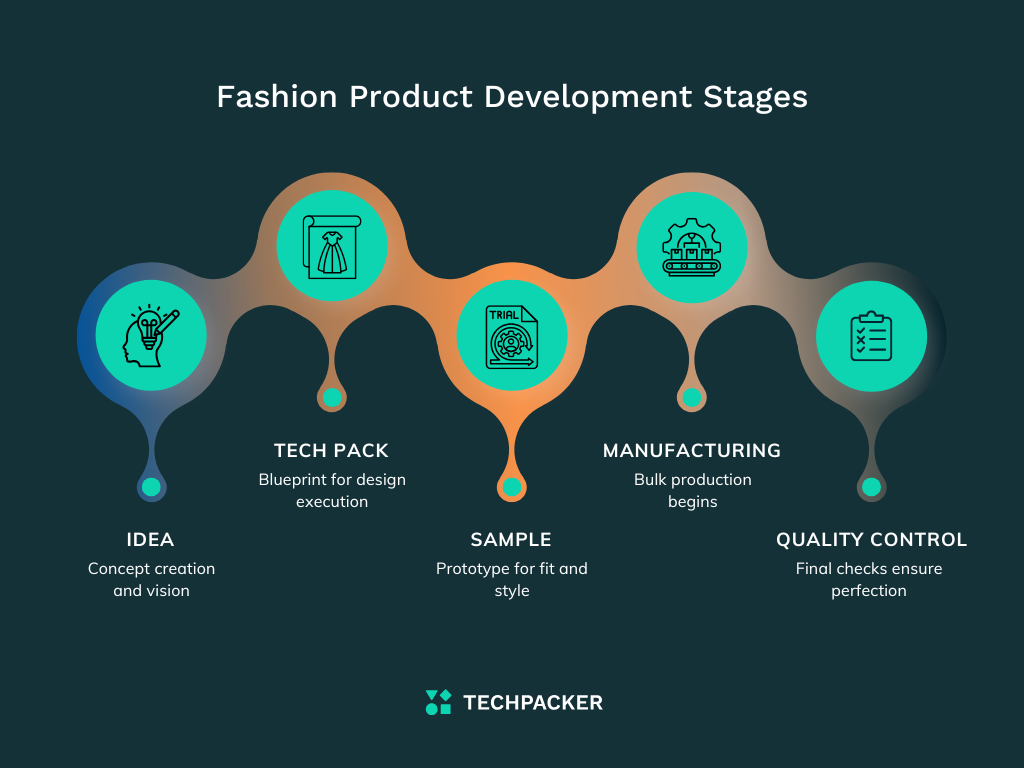
Visualizing an idea
Once the designer or the design team comes up with an idea it is time to visualize it. The two most common ways to visualize an idea are:
- Creating a mood board and getting inspiration from the existing designs.
- Drawing a few sketches for different versions of the design.
Very often both of these ways work in tandem. The design team creates a mood board, takes inspiration from some details of the sisting design, adds new elements to it, and creates a brand new product.
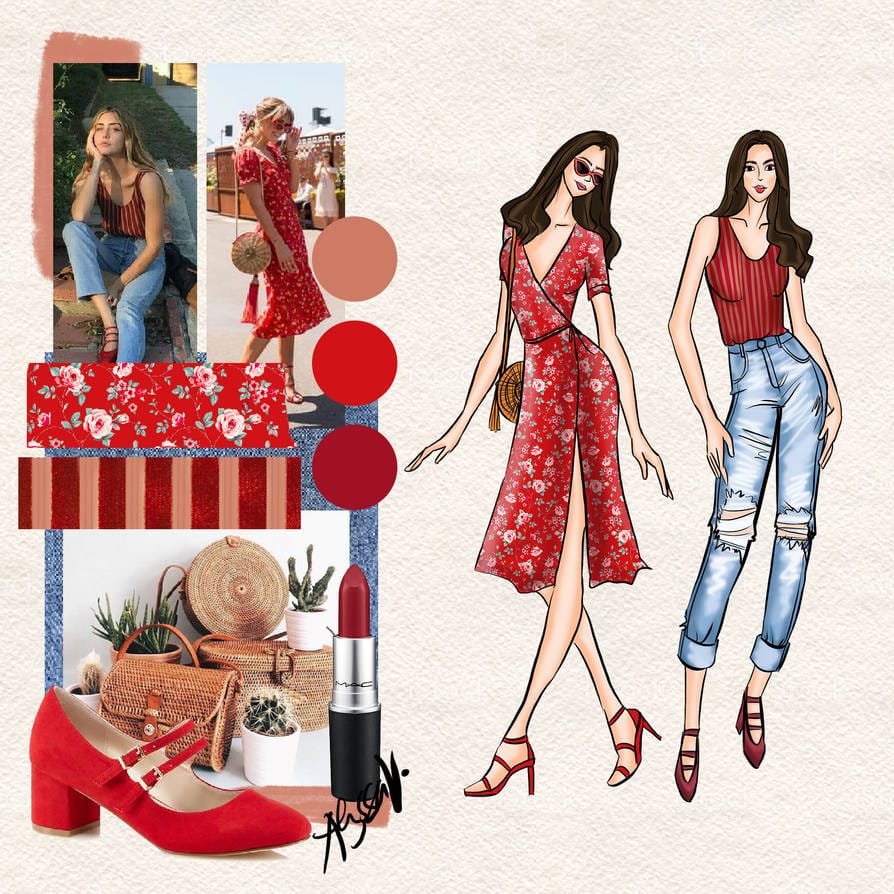
The very first design sketches usually are drawn on paper. All design team members brainstorm together and add their input. After numerous rounds of approval, they have their final product design, including colorways, fabric swatches, other accessories, and trim details.
Based on that the technical designer creates fashion flats or technical sketches. The main purpose of the technical designer is to communicate their design idea to the manufacturer, including the technical aspects of it. Like seam lines, darts, accessories and trims placements, and other construction details. The result is a flat sketch of an actual manufactured garment.
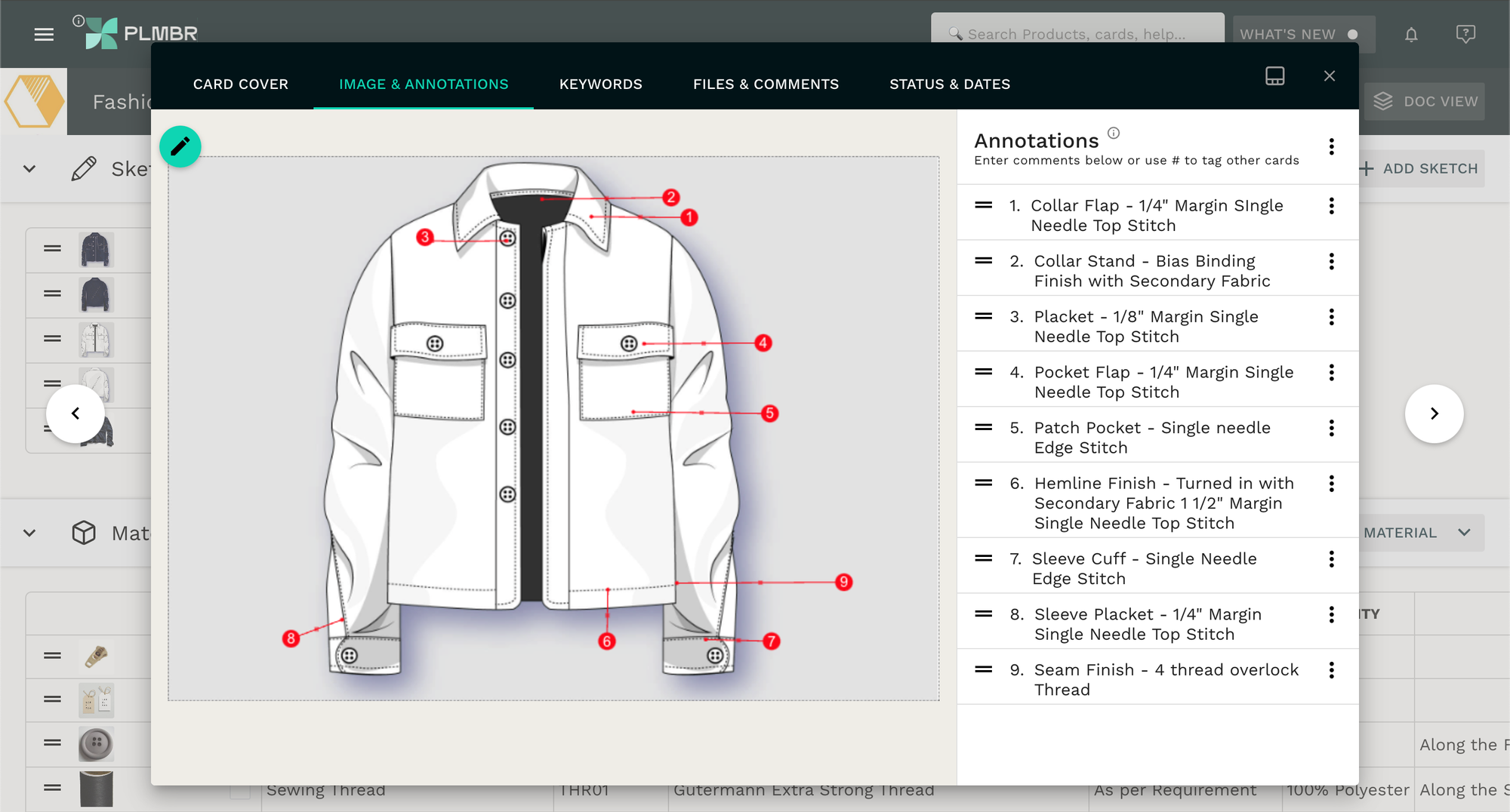
Fashion flats are complex and need to be very detailed, otherwise, the garment might not come out as expected. Check out our guide on how to ace your technical flat sketches.
If you don't have the skills to create technical sketches from scratch, you can also create fashion flats by repurposing Repsketch pre-made vector sketches.
Once the concrete concept has been developed, you can move forward to the next product development step.
Sign up for our FREE membership and get access to
All premium articles
E-courses and ebooks
Ad-free experience
Tech pack templates
Tech pack development
Consider the tech pack as a “blueprint” for the manufacturer on how to produce your garment. It is a design document that includes sketches and specifications of the proposed clothing product. Including materials, accessories, and trims that will be used for its manufacturing. The main purpose of the tech pack is to help suppliers assess if the fashion product is doable and ready for manufacturing.
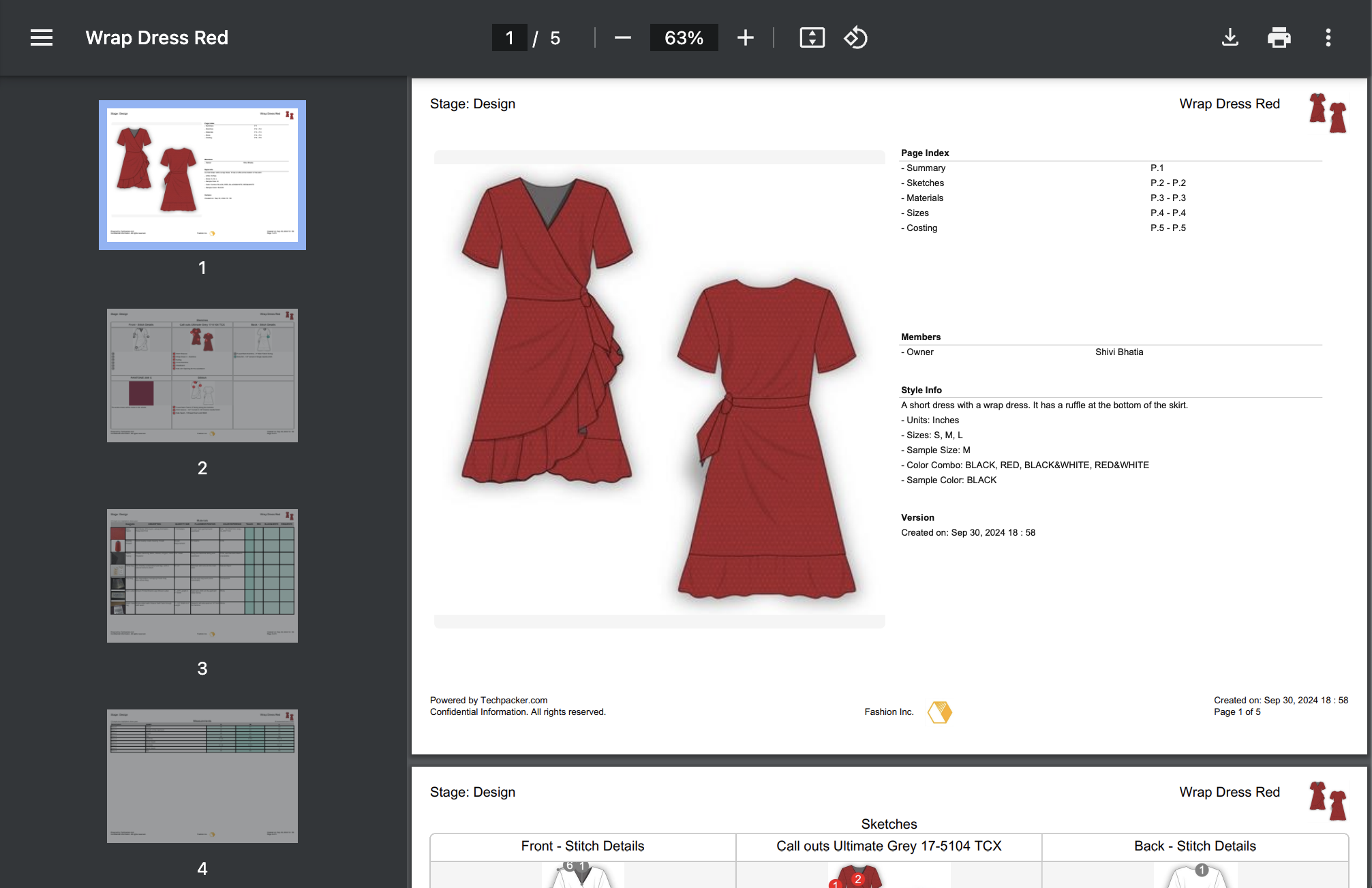
Developing a comprehensive and easy-to-read tech pack benefits every fashion business in many ways:
- It helps get an accurate price quote from your supplier.
- It helps get error-free samples.
- It helps improve fit quality.
- It works as a reference point for quality control.
Apart from that, a tech pack can be transformed from a mere document to a collaborative environment where designers, product developers, buyers, and quality control planners work together to create better products faster.
A fashion specification sheet or cut sheet is an important part of every tech pack. It contains all of the important measurements needed by your clothing manufacturer. For example, the length of the garment, chest, waist, and hips measurements. A typical spec sheet includes a variation of the measurements for different sizes (like S, M, L, XL, and so on).
Point of measurement (POM) diagrams is used to visually represent your garment’s measurements. To create POMs, designers draw arrows call-outs to show exactly where each measurement is on the garment. These are usually drawn in Adobe Illustrator along with the technical sketch of the garment. Techpacker lets you add callout annotations simply in one click while building your tech pack without jumping back and forth between the platforms.
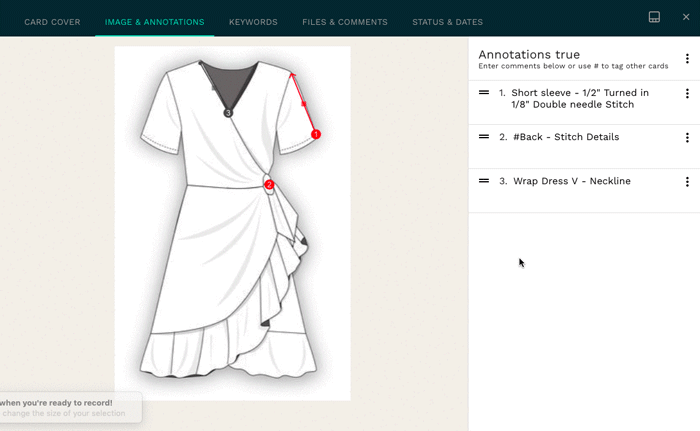
Next, we grade the garment for different sizes. Software that develops Tech packs, like Techpacker, completes this auto-grading for you based on the rule you provide. This helps speed up the process and avoid mistakes.
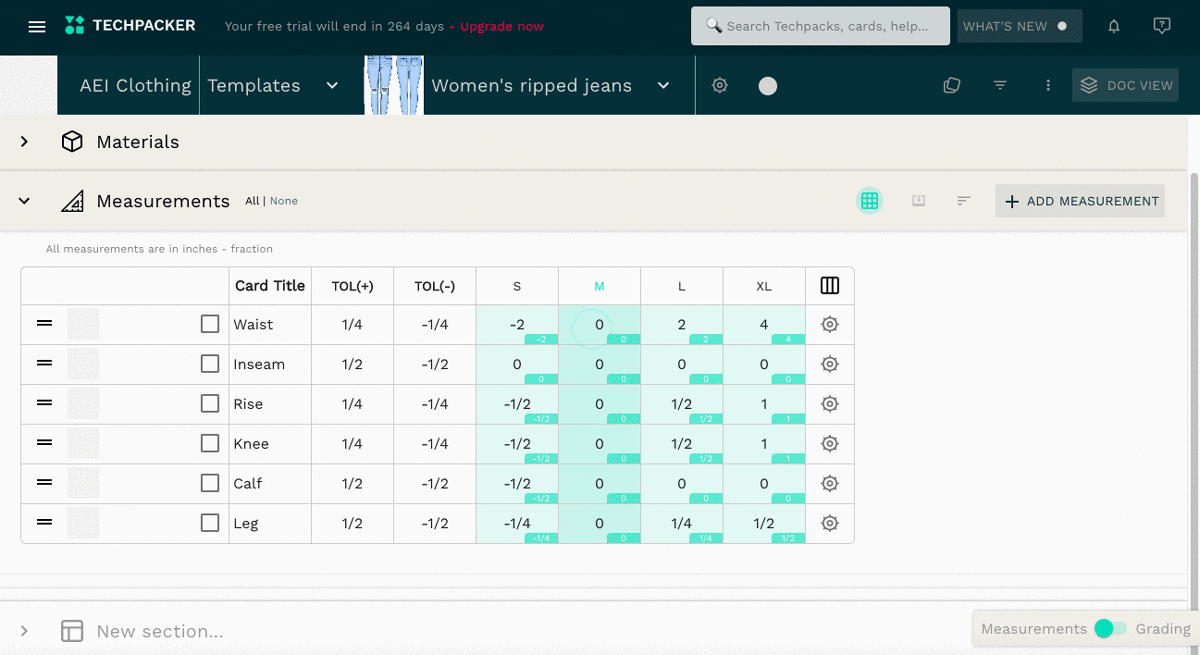
Sample making
Design teams collaborate with the manufacturer to create the first version of the garment. The goal of making samples is to see how the garment will look in real life. It is also used for fitting purposes, to see how the garment fits on a target size model.
Normally it takes several rounds of sample making until the final sample is approved. The design team might request minor tweaks like measurements adjustments or decide to change some design details like using a different types of fabric for example.
After developing the first sample, the specification sheet may be revised. If any edits are needed the changes will be reflected in the initial spec sheet. Then all the edits and comments are incorporated to modify the sample. The final sample will become the basis for the final version of the garment.
Sample-making can be considered the pre-production stage of the manufacturing process. In total, there are 12 types of samples in apparel production.
Manufacturing
Clothing manufacturing includes numerous operations necessary to make a garment. It includes processes like cutting, sewing and finishing. The whole manufacturing process breaks down into a number of sub-operations needed for constructing a particular garment. Some of these operations vary depending on the type of equipment available, work methods used, and workers’ skills.
After the final sample is approved and the materials are sourced the time has come to produce the whole run. Depending on the type of factory that you work with, they might offer a full production package and help with materials sourcing and packaging.
Clothing manufacturing consists of the following stages:
- The pre-production stage includes materials sourcing, pattern making, and sample-making that we discussed previously.
- The production planning stage makes sure that all manufacturing activities are completed on time.
- The cutting process uses the guidelines provided by the designer.
- Manufacturing of the whole run based on the Purchase Order Sheet provided by the design team.
- Delivery of the final order.
Quality control
Quality Control is generally understood as assessing the quality of products upon completing manufacturing and after being classified into acceptable and unacceptable categories where checking of the actual results is done to ensure that things are as expected.
Apparel quality control is performed with the help of tests, checks, and inspections to ensure clothing products are made with the best standards and according to the intended design and correct specifications.
Some of the main factors when judging the quality of a garment are:
- The difference between color shades;
- Fabric defects like the quality of fiber;
- Construction defects like exposed notches, loose threads, or stains;
- Measurements differences.
In addition to that, quality control may include packaging and labeling inspection. The garment quality control checklist should be created before production begins. It will be then used on-site as a reference guide for the manufacturer throughout the production.
Tech Pack and Spec Sheet are the main reference points for quality control. The quality control inspector makes sure that all design details of the physical garment correspond to the specifications in the tech pack.
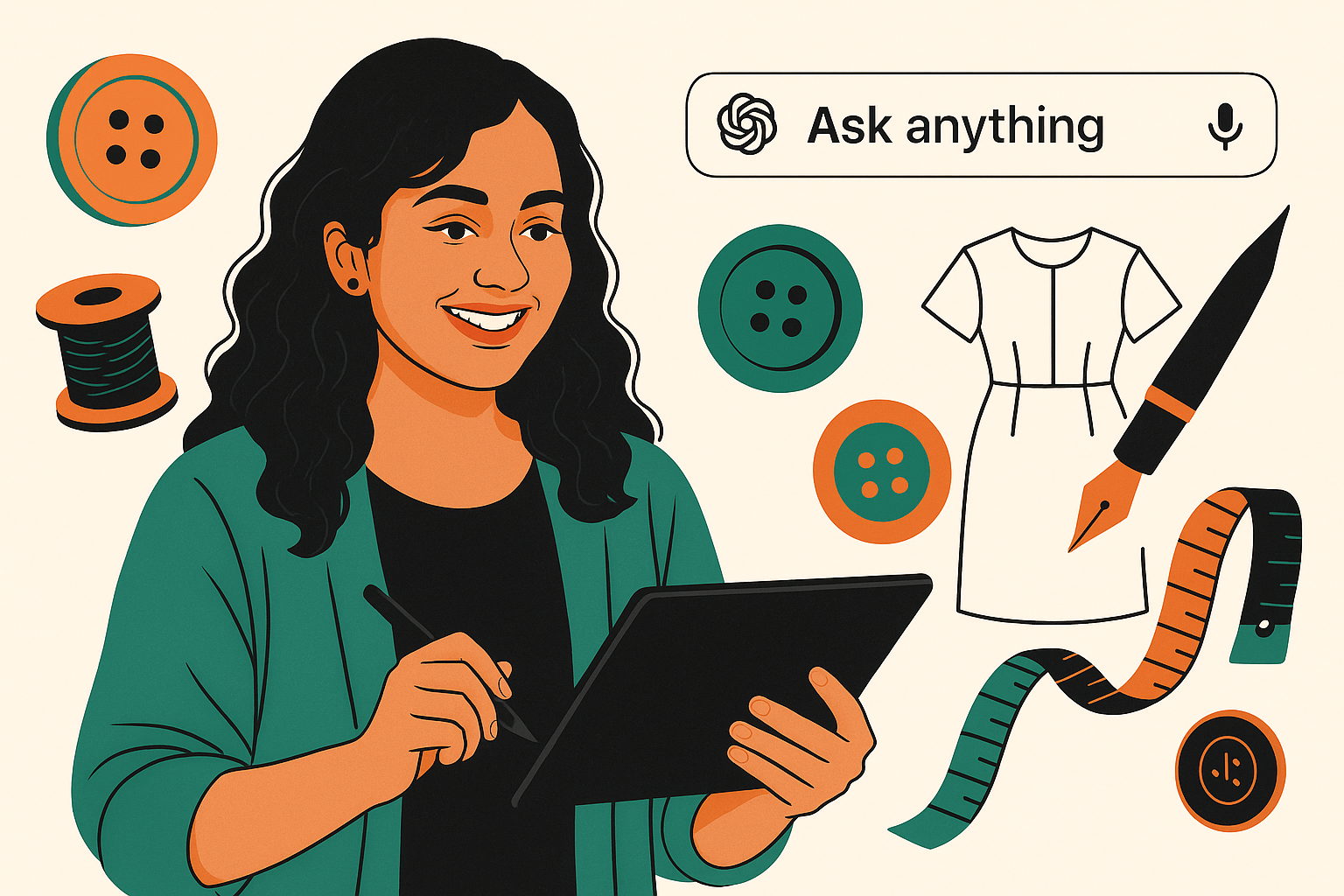
The role of a product developer in fashion
Fashion product developer plans, develops, and presents fashion products for a target market within a company. They work closely with technical and design teams to develop seasonal collections. The main goal of the fashion product developer is to focus on quality and to make sure the fashion house and the consumer are happy with the product.
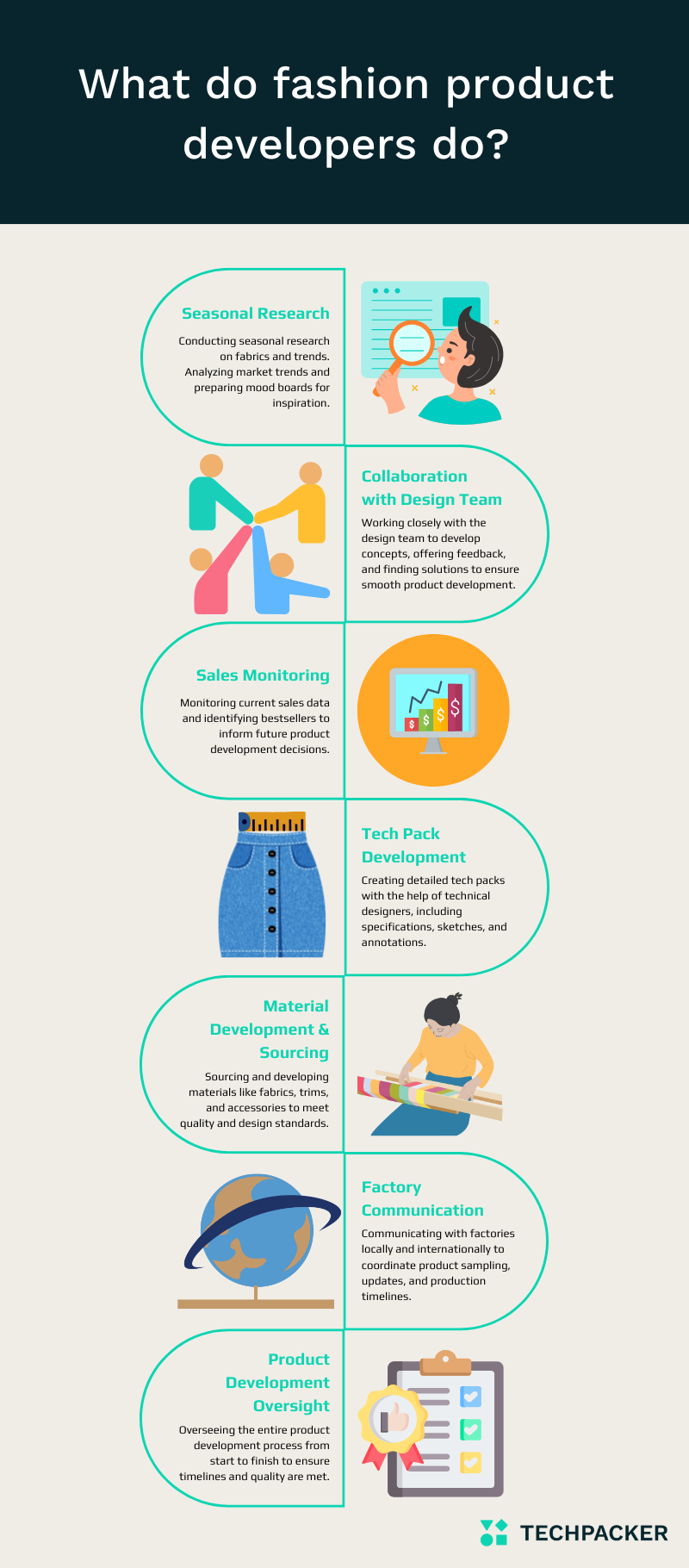
Daily tasks of a fashion product developer include:
- Conducting seasonal research on fabrics and trends;
- Working closely alongside the design team to develop a design concept and offer insightful feedback, ideas, and solutions to make sure product development runs smoothly;
- Monitor current sales and keep a close eye on bestsellers;
- Developing tech packs with the help of technical designers;
- Material development and sourcing;
- Communicating with different factories locally or internationally;
- Overseeing the whole product development process from start to end.
Fashion product developers need to have a great understanding of the design process. As they need to work closely with designers to interpret their creative vision into a technical document (tech pack) that can explain the vision to manufacturers and suppliers. Product developers have to be able to confidently communicate specifics from pattern cutting and construction to raw materials to suppliers.
Fashion product developers have great time management skills. They ensure collections are delivered on time and all product development stages stick to deadlines.
Fashion product developers oversee the entire production line, they have key operational knowledge of factories and excellent communication skills to share important information effectively and clearly across the production process. Product developers are proficient in all-important design software from Excel to Illustrator.
Fashion product development software
Modern fashion product development software makes Product Lifecycle Management (PLM) more efficient and the whole supply chain more transparent.
PLM software is an information management system that manages data during the development of products from concept to manufacturing. The main purpose of the PLM solution is to provide a central place for managing the product lifecycle efficiently and cost-effectively.
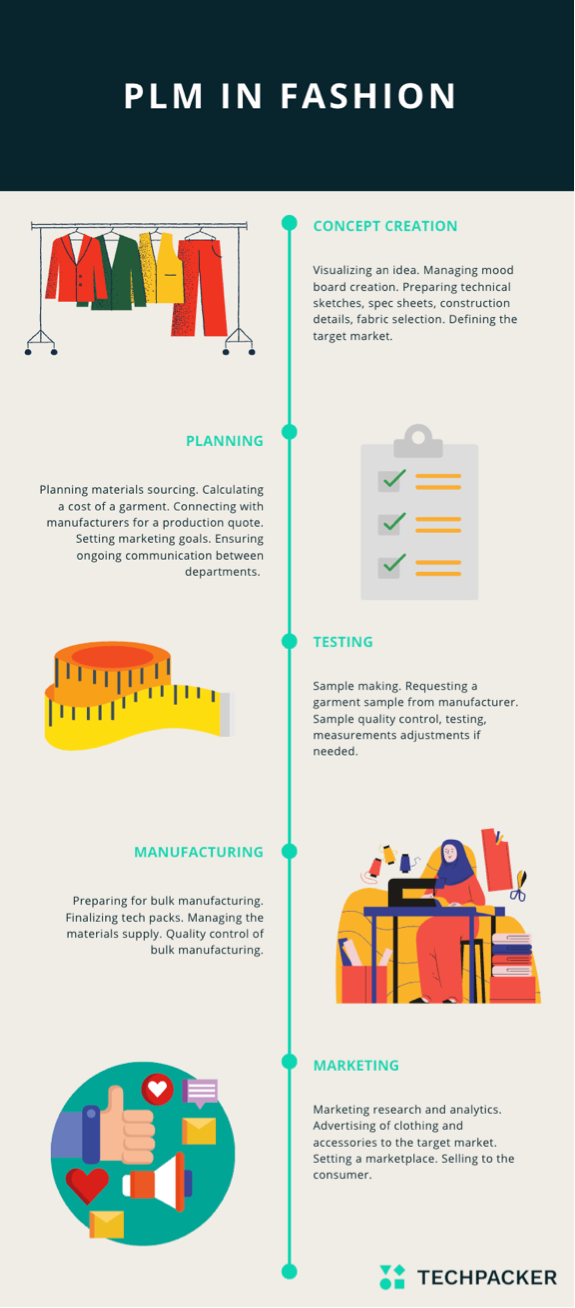
PLM software was once a luxury that only big fashion brands could indulge in. Although, now even small fashion brands are embracing PLM solutions to optimize their supply chain.
There are many different PLM software to choose from depending on your fashion business size and goals. Some of them are more affordable than others, some work better for growing businesses while others focus on small teams, some are easier to use while others require special training, etc.
There are many benefits that PLM software provides to fashion businesses:
- Easy integration with Adobe Illustrator, Excel, and other industry-leading software;
- Multi-channel communication between the design team and other members of the supply chain;
- Secure data storage that can be easily re-used;
- Unified collaborative environment;
- Tools to track, control and oversee the product development stages.
However, the implementation of the PLM software comes with its own challenges. Many PLM software was not designed for the fashion industry so they are not visual enough when it comes to product development. Some PLM solutions exclude manufacturers from the product development process. Which makes the sample-making and manufacturing process challenging and prone to mistakes. Struggling to learn a new system is another challenge, training design teams takes time and money.
Despite the challenges, PLM systems improve visibility and data flow across the company and the entire supply chain. Fashion industry experts see the PLM software as a solution that makes the industry more relevant, smarter, and more adaptable.
To sum up, fashion product development involves the process of conceptualizing, designing, creating, producing, and delivering new products to consumers. Design teams of all sizes are adopting modern software to help them run the process smoothly and efficiently. Learn how Techpacker can help!
Other basic FAQ's
1. How can I use AI like ChatGPT in my fashion product development workflow?
AI tools like ChatGPT can be integrated across multiple stages of the product development process—from idea generation and trend research to creating mood boards, drafting tech packs, and even communicating with manufacturers. By automating repetitive tasks and offering creative suggestions, ChatGPT enhances both speed and precision.
For a detailed, real-world guide, check out our blog: How I Use ChatGPT to Speed Up Fashion Product Development
2. What are tech packs and why are they essential for product development?
Tech packs are detailed documents that communicate every technical aspect of your fashion product to manufacturers—from design sketches and materials to measurements and construction details. They serve as a blueprint for turning ideas into actual garments. However, traditional static tech packs can slow you down.
Learn why modern digital tech packs are a game-changer: Why Tech Packs Don’t Work Anymore – Secrets to Successful Product Development
3. What causes delays in fashion product development, and how can I avoid them?
The most common bottlenecks include miscommunication with suppliers, lack of version control, disorganized file sharing, and delayed sample approvals. These inefficiencies can cost you weeks—if not months—of lost time.
Explore actionable solutions in this article: Top 4 Product Development Bottlenecks Impacting Time-to-Market
4. How can fashion businesses streamline communication with manufacturers?
Clear tech packs, centralized file management, and automated change tracking significantly reduce back-and-forth emails and sampling errors. Using platforms like Techpacker allows real-time updates, which means your factory always has the latest version.
Here’s how to automate product development updates: How to Automate Product Development Changes
5. What are the best tools for fashion designers in 2025?
In 2025, designers are turning to AI assistants, cloud-based PLM systems, mood board creators, and mobile sketching apps to stay efficient and inspired. Combining these tools enables designers to streamline workflows, stay organized, and reduce manual work.
Get the full list of must-have tools:
15 Apps For Every Fashion Designer in 2025
Quick and Easy Design Tools for Every Product Developer
6. How do I find a good freelance designer or fashion design agency?
Working with experienced freelance designers or agencies can help elevate your designs while keeping your team agile. Whether you need CAD sketches, tech packs, or collection planning, many top professionals specialize in remote, project-based work.
Discover vetted experts here: Top Fashion Designers and Design Agencies | Expert Fashion Services
7. What is consumer-centric product development in fashion and why does it matter?
Consumer-centric development means designing with the end-user in mind—factoring in their lifestyle, preferences, values, and pain points. It’s not just about aesthetics; it’s about problem-solving through design. This approach often leads to better-selling, more meaningful products.
Explore how to embed this thinking into your design process: Understanding Consumer-Centric Product Development in Fashion
8. What’s the role of PLM in scaling a fashion business?
A PLM (Product Lifecycle Management) system acts as the backbone of your operations, helping you centralize product data, collaborate with teams, and reduce time-to-market. For small and scaling fashion businesses, implementing the right PLM can significantly improve productivity and output.
Dive into our complete guide:
The Ultimate Guide to PLM for Fashion
How to Scale a Fashion Business With Clear Product Development Processes